September
1999 Article 3
MPE
INDUSTRIAL ATTACHMENT STUDENT WINS TOP PRIZE IN SEAGATE TECHNOLOGY INTERNATIONAL’S
INTERNS PROJECTS COMPETITION
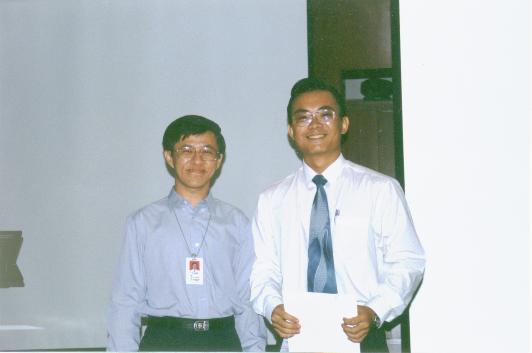 |
Wilson
Oh (MPE) (on the right), First Place Winner with Mr T H Chee, Vice President,
Drive Engineering Asia Pacific, Seagate Technology International
|
This
year Seagate Technology International started a project competition to
foster creativity among their interns from both NTU and NUS. They
also wanted to encourage the students to learn presentation skills, etc.
More importantly, through this program, they wanted to identify good potential
employees.
A
total of 69 interns from both NTU and NUS, attached to the various plants
took part. The competition involved 3 rounds. The first round
was on an Intra-plant level, the second round, on an Inter-plant level,
and the top five qualifiers presented their projects at the Finals.
The panel of judges comprised academics from NTU and NUS and also Directors
from the various plants. Mr Wilson Oh walked away with the Top Prize
of $500. He had undergone the School’s Leadership Development Program
which was introduced to identify and develop potential leaders among the
“cream of the crop.”
Mr
Oh was attached to Seagate Technology International Customer Service Operations
(CSO), from 11 January to 26 June this year, as part of the School’s Third
Year Industrial Attachment program. During his stint with CSO, he
was assigned to the Department of Industrial Engineering and Strategic
Planning. He handled many projects, ranging from process improvements
to plant layout. However, throughout the period of attachment, he
had the challenging task of identifying and investigating the problems
with the plant operations. This was indeed a mega-scale project.
Having
carefully identified and performed a thorough investigation, Mr Oh developed
a new system for the plant operations. This involved the flow of
materials, as well as the merging of some of the functional areas.
The advantages of the new system include a reduction in the level of inventory,
improvements in the cycle time, and better management of Work-In-Progress
(WIP). All these contribute towards making the factory more “lean”,
in line with the organizations drive towards “Lean Manufacturing”
A
presentation was made to the top management and the new system was accepted
and implemented in various phases. The initial phase of implementation
saw a substantial decrease in the level of excess inventory.
Subsequent implementations are currently in the pipeline, and with such
promising results, this new system may very well be implemented in other
Seagate plants with similar operations.
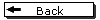 |
|