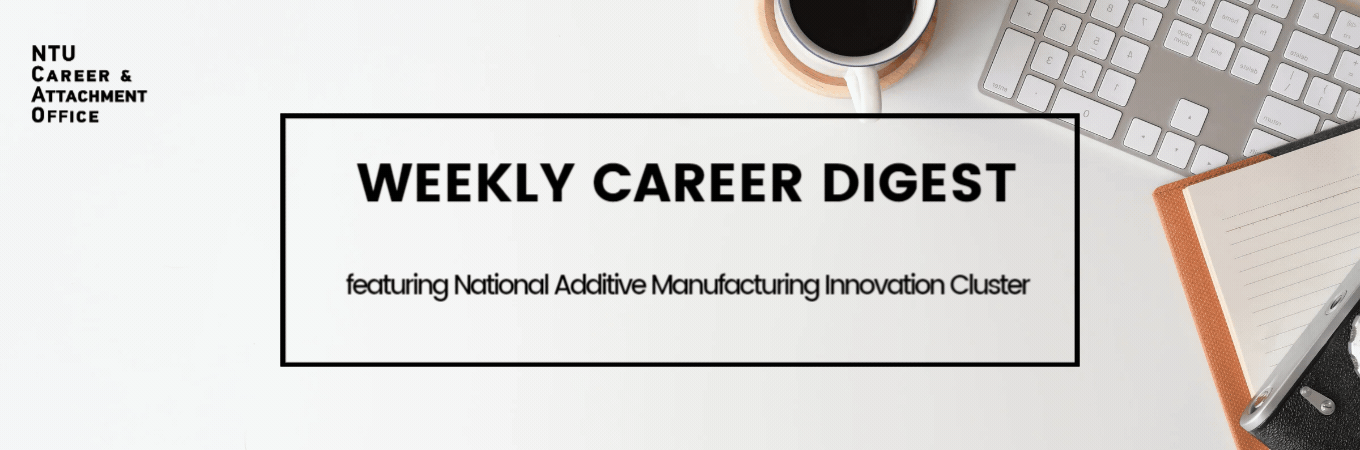
Bioprinting and Biocompatible
Materials –
Re-defining a New Era of
Applications With 3D Printing
|
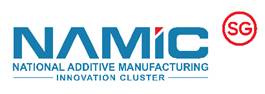
|
By National Additive
Manufacturing Innovation Cluster featuring:
-
Dr
Lim Yujing, CEO & CTO, Osteopore,
PhD (BioEngineering, NTU)
-
Mr Linhan
Wu, Principal (Education and Community), Hyperganic,
Bachelor (Communications and Information, NTU)
-
Mr Lim Woon Yong,
Research Engineer, AM.NUS, Bachelor (Engineering, NTU)
|
Dear Students,
Advances
in 3D printing techniques and materials research have enabled physicians, clinicians,
surgeons, and scientists to develop new treatment strategies and medical
devices for biomedical applications. These advancements in 3D printing have
introduced us to a new branch of medical therapy, Regenerative Medicine.
In
this edition, we are focusing on Bioprinting and Biocompatible materials.
Bioprinting technologies and biocompatible materials have enabled researchers
and clinicians to develop biocompatible implants, scaffolds, organoids,
prosthetics for biomedical applications. Let us explore the latest
developments from promising Singapore-based MedTech enterprises that are
redefining a new era of Regenerative Medicine and Tissue Engineering.
Osteopore (ASX: OSX)
A Global Leader in Regenerative
Medicine Solutions
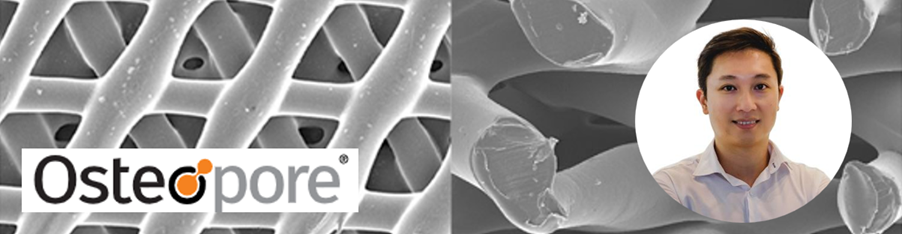
Integrating
the science of Tissue
Engineering and Regenerative Medicine with 3D printing technologies to
design, develop and manufacture implantable devices – Osteopore
(ASX: OSX) is a Singapore-based medical technology enterprise specialising in
providing Regenerative Solutions for biomedical applications.
Helmed
by Dr Lim Yujing, CEO & CTO, Osteopore (PhD. NTU) and his team, Dr Lim will share
how he got started on this journey of running a medical technology
corporation.
The
implant market of the medical device industry is vibrant, dynamic, and
driven by a constant influx of surgical innovations designed to augment
clinical outcomes and patient experience.
Osteopore is a pioneer
in the area of regenerative bone healing by 3D microstructures. Our deep
understanding of how bone heals have enabled us to design, 3D print, and commercialise bioresorbable bone implants
that make a difference in clinical outcomes and patient experience.
With
the support of specialist surgeons working in craniofacial reconstruction
and augmentation, Osteopore has achieved more
than 100,000 implants in patients, demonstrating safety and
effectiveness for more than 15 years.
|
As
we continue to grow, we strengthen our understanding and develop solutions
for other tissue reconstruction needs such as cartilage and tendon.
In
addition, we continue to expand our clinical applications beyond the craniofacial; going into rhinoplasty, dental, and
orthopaedics. Working in this exciting field requires a broad-based
understanding from several academic disciplines, including engineering, the
sciences, and medicine. While classroom learning provides a foundational
knowledge, continuous experiential learning through research,
experimentation, commercialisation is equally important.
Gaining
experience through internships and part-time jobs is highly beneficial.
Additionally, opportunities to work with research groups focused on tissue
regeneration should be considered.
|
In
research, it is important to identify clinical needs to guide the
development of appropriate solutions – this can often be achieved by
working with specialist surgeons who can better identify and describe the
clinical challenges that they face. We look forward to the next innovation!
Author: Dr Lim Yujing, CEO & CTO of Osteopore (ASX: OSX). Dr Lim holds a Masters
of Engineering from NUS and PhD (Bioengineering) from NTU. He has
more than 10 years of research experience in Tissue Engineering and
published extensively in internationally peer-reviewed journals.
Photos sources: https://www.osteopore.com/
https://www.linkedin.com/in/yujing-lim-19b40046/
|

|
Revolutionising
Hip Joint Implants with Advanced Lattice Design for Optimal
Osseointegration and Weight Reduction
|
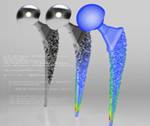
|
By Linhan Wu,
Principal, (Education and Community), Hyperganic;
Bachelor of Communications and Information (NTU)
|

|
|
|
|
The
Challenge: The primary challenge in hip implant
design is optimising structural integrity and weight to improve both
longevity and comfort for the patient, while also ensuring rapid
osseointegration. Conventional design workflows are not only time-consuming
but also limited in their ability to iterate quickly and explore a wide
range of design configurations.
Our
Approach: Leveraging Hyperganic
Core, our team employed a novel approach that integrates quasi-meshless
simulation with algorithmic engineering. This method allows for the
automatic generation and evaluation of complex lattice structures within
the implant. We adopted a Grow-as-you-go workflow, which utilises a
feedback loop to refine the implant design iteratively based on simulated
performance data.
Stochastic
Lattice Optimisation: The stem of the hip joint implant was
designed using a stochastic lattice structure. The algorithm calculated
optimal beam thickness by simulating the stresses the implant would
experience under typical loading conditions. This ensured the implant was
strong where necessary but not excessively heavy.
|
Topology
Optimisation: The design process incorporated
advanced topology optimisation to minimise material use, while maintaining
essential structural properties. This approach adjusted the density and
orientation of the lattice beams dynamically, aligning the material
distribution closely with stress distribution patterns.
Solution:
The integration of Hyperganic
Core's capabilities transformed the design process.
Performance-driven
Design Iteration: Each design iteration was informed by
previous simulation results, allowing the implant to evolve towards an
optimal structure. This method reflects natural evolutionary processes,
where iterative trials refine biological structures for improved performance.
Reduced
Design Time: The new workflow significantly cut
down the design cycle time. What traditionally took months in iterative
testing and redesign could now be accomplished in weeks, with each
iteration taking place in a fraction of the time required by traditional
methods.
|
Enhanced
Implant Performance: The final implant design achieved a
balance of reduced weight and increased durability. The optimised lattice
structure provided superior load-bearing capabilities and improved
integration with bone tissue, promising a higher success rate in clinical
applications.
Conclusion:
The application of Hyperganic
Core’s algorithmic design and quasi-meshless simulation marked a
significant advancement in the field of medical implants. This case study
not only demonstrates the potential for sophisticated digital tools to
enhance medical device design but also sets a new standard for the rapid
development of customised implants that better meet the needs of patients.
Author: Linhan
is Principal (Education and Community) at Hyperganic,
a German-Singapore physics-driven engineering software startup, where he
champions technical marketing, communications, and developer relations.
With experience in innovation management, deeptech
venture building, and education technology, Linhan
is a multi-disciplinary communicator who harnesses the power of business
and design to build a better tomorrow.
Source:
https://www.linkedin.com/in/wu-linhan/
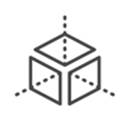
|
Ideation to
Reality: Development of a novel 3D printed Titanium Alloy 6-4 Hip Implant
|

|
By: Lim Woon Yong, Research Engineer, AM.NUS
(under guidance of Prof Sing Swee Leong, NUS)
Bachelor of Engineering (NTU)
|
Woon Yong's inspiration journey began
when he was an undergraduate in NTU School of Mechanical and Aerospace
Engineering with a simple yet profound question: How can we lighten
the part weight without compromising the mechanical properties? Fueled by
curiosity and a desire to make a meaningful impact, he set out on a path that
would lead him to the forefront of orthopedic prothesis design. Recognising the potential of additive manufacturing and
advanced materials, Woon Yong envisioned to develop an intricate hip implant
that combined strength, durability, and biocompatibility.
With years of experience in researching
the uses of titanium alloy in biomedical applications and a passion for
pushing the boundaries of medical device innovation, Prof. Sing Swee Leong
provided Woon Yong the wisdom and direction needed to navigate the complexities
of hip implant design. Under his mentorship, Woon Yong gained insights into
further development of the hip implant by using Hyperganic
simulation, Materialise Magics software, and 3D
printing as fabrication method. Titanium alloy 6-4 was chosen as the choice
material due to its desirable properties such as biocompatibility, high
corrosion resistance and high stress tolerance.
Woon
Yong redesigned the femoral head joint from solid to open lattice structure,
added a shell to convert the solid sphere to hollow structure. Materialise
Magics software was used as a final finishing touch to generate the open
lattices.
Finally,
Woon Yong printed the hip implant using Renishaw Ren500M (housed in AM.NUS) which abides by
ISO13485 medical devices standards. ISO 13485 served as Woon Yong guiding
framework, ensuring that every aspect of the project – from design and
development to manufacturing and post-processing – adhered to the highest
standards.
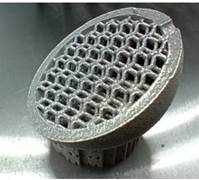
|
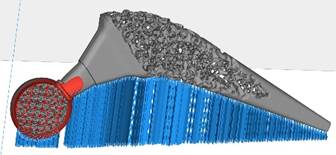
|
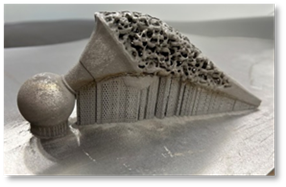
|
3D printed cross section of the sphere
(femoral head)
|
Selected sectional view of femoral head
(Materialise Magics
View)
|
Final 3D printed titanium alloy hip implant
|
Author:
Lim Woon Yong is currently serving as a Research Engineer in AM.NUS.
He is an alumni of NTU, holds a Bachelor of
Engineering (NTU) and obtained ASTM Professional Certificate Course in AM.
Woon Yong had 6 years of research experience in development of biomedical
devices, Additive Manufacturing, Metallurgy and Engineering Design in local
research institutions.
Source: https://www.linkedin.com/in/woon-yong-lim-984b5a158/
|
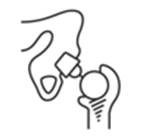
|
If you are interested in additive
manufacturing, now is an exciting time to explore a career in this dynamic
field. You too, could be part of these groundbreaking changes that impacts
patient care and technological advancements.
Follow
NAMIC on LinkedIn and visit their website for the latest industry updates.

|